You can’t manage or improve what you can’t see. That adage is never more appropriate than when it comes in inventory. Whether you do it yourself or rely on a combination of third-party suppliers or service providers, inventory management, tracking and measuring utilization, trends, and inventory movement across thousands of stockkeeping units presents a perpetual challenge.
Building a reliable process for managing your inventory and warehouse procedures can introduce across-the-board efficiencies that come with dedicated oversight, regulated workflow, and sophisticated analytics. There are two primary visibility goals:
1. Constant Parts/Goods Availability
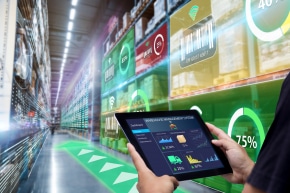
Fulfillment – whether it’s delivery or pickup of a consumer good or the linesiding or installation of an industrial component – is the hallmark of customer service. Omnichannel commerce and various supply chain/procurement partners create complex networks with several endpoints from which supplies and goods can emanate. The visibility achieved through inventory management is critical in knowing which resources are available and what to do about the ones that aren’t.
Retailers and manufacturers should insist their third-party inventory management partners open up to data exchange with aggregated supply sources to illuminate parts availability across the enterprise. Perhaps the only thing worse than not having a replacement on hand when a critical part fails or a popular product leaves the shelf, is having one but being unable to locate it.
2. The Shortest Lead Times Possible
Visibility into lead time, the number of hours or days that elapse between the time a purchase order is placed and the goods arrive, enables manufacturers and retailers to prevent and solve a range of potential bottlenecks. By understanding your own and each supplier’s manufacturing schedules and delivery routes, you can work with your inventory management company to develop contingency plans in case disruptions occur in sourcing, receiving, warehousing, and shipping your inventory.
The COVID-19 pandemic and resulting shipping dock backlogs drove this point home, but the global nature of the supply chain for many industries continues to pose geopolitical, weather, human, and market threats. Lead times and potential delays dictate how much safety stock it is prudent to keep on hand.
Comprehensive, real-time visibility enables efficient scheduling, ordering, staging, and warehouse practices to minimize stockouts and maintain service levels within organizations.
Third-party Inventory Management Improves Visibility
Engaging with your third-party service providers in inventory management is not something you can just set and forget. But it’s a deeper collaboration in order to leverage a vendor’s expertise and facilitate optimal in-house resource management. Gaining visibility into inventory managed by third-party service providers oftens bring established best practices and expertise across industries that can streamline inventory and warehouse operations, such as:
• Aggregated Data – combining results from various clients enables third-party inventory management companies to create statistically significant sample sizes for identifying consumer demand patterns for finished goods and predicting failure rates for maintenance, repair, and operations supplies, for example.
• Fewer Stockouts – Third-party inventory management aggregators implement robotic process automation, machine learning, artificial intelligence, and other sophisticated tools to provide visibility to shift goods and machine parts between locations as demand warrants.
• Optimal Inventories – Closely monitored stock levels and programmatically reordered supplies enables real-time insights into the three key questions every warehouse manager needs to know: How much do we have? Where is it? How long will it take to get it where it needs to be?
• Robust Analytics – Knowing when, where, and how much an inventory item is used empowers more precise demand forecasting, maintenance scheduling, and promotional strategies.
• Less Waste and Cost – A central warehouse or distribution center can make sure you don’t overorder. Keeping too many units in storage risks them becoming obsolete, failing to move in a timely manner, and take up valuable space needed for new products.
• Delighted Customers – An inventory management company can ensure adequate inventory to fill customer orders. Few experiences are more frustrating for e-commerce shoppers than finding the perfect item just to learn that it’s on backorder.
SDI Inventory Management Solutions
SDI gives our supply chain partners the freedom to make optimal decisions unshackled by worries of the efficacy and visibility of their inventory operations. With SDI on the job, they can rest assured that their facilities will maintain lean but adequate inventories served by responsive suppliers so they can enjoy the flexibility that gives them a competitive advantage.
SDI puts its proprietary software and time-tested processes to work for you to generate high-ROI cost savings and revenue opportunities. Talk to one of our inventory management experts to see how SDI’s integrated services can illuminate your warehouse and supply chain processes.