The “next normal” in facility management is already here, and the perfect storm is on the horizon. FM leaders, already resource-constrained by the pandemic and early retirements, are facing continued labor shortages over the next two to four years as aging baby boomers exit the workforce, widening the skilled labor gap. The International Facilities Management Association (IFMA) estimates that 40% of existing facilities managers will retire by 2026. This generational shift in the FM workforce will leave an estimated 158,000 positions unfilled by 2026.
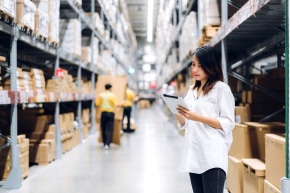
According to a recent FM Training Outlook Survey by ProFMI, The Professional Facility Management Institute:
● 66% of FMs and staff have left or have considered leaving their job in the past year
● 54% of corporate leaders expect to have open FM-related positions at all levels of the organization this year
● 86% of FM employers say there’s a gap between their team’s current knowledge and skills and what they need to excel
Labor shortages in facilities management have cast a spotlight on FM supply chain technologies that augment FM teams to help ensure facilities and revenue-generating assets are maintained and repaired as quickly as possible. Aligning the facilities function with broader organizational supply chain management and enterprise asset management strategies creates end-to-end visibility to drive improvements in the lifecycle of these mission-critical assets that impact the in-store customer experience.
Managing Supply Chain for How FMs Work
Multi-site facilities leaders have the challenge of managing brick-and-mortar facilities spread across geographical regions. Whether the technicians are contracted through a third party, or whether the organization has an in-house team of mobile maintenance techs, work orders are typically assigned by territory. Because work orders are assigned by radius alone, unless the job is for specialty trades (HVAC/R), labor resource allocation doesn’t factor in the availability of materials to complete the work order, current truck stock levels, labor rates, or even technician skill requirements.
By adopting FM supply chain technologies and solutions, organizations are empowering their field technicians to use a single mobile app to order many of the common items they need, while standing right in front of the equipment on the job site. They also have access to bill of materials, quick reference guides, and manuals on the equipment they’re servicing, right in the app. This saves a tremendous amount of time in going back to the truck or shop to locate a manual.
Key features to look for in FM supply chain technology:
• Single payor platforms – Technicians can better manage their time by completing all their purchases in one location.
• Supplier call-in – Technicians place orders for pick up at their preferred local supply branches, and better plan maintenance schedules and routes.
• Punch-out – Access catalogs and inventory across the supply chain ecosystem via punch-out technology to consolidate shopping carts into one central platform. Watch this quick video on how the punch-out feature of SDI’s IPM App helps mobile maintenance technicians reclaim 1-2 hours of their day.
• Real-time data visibility and notifications that allow technicians to plan their maintenance work orders around the delivery schedules of the needed materials.
• Interoperability – Integrate via API with work order management or computerized maintenance management systems to connect purchase orders (and lead time data) to the corresponding work orders, which provides benefits in productivity downstream as well as provides cross-reference data for kitting suggestions to further reduce mean time to repair.
Improving Enterprise Visibility to Drive Results
For any multi-site facilities leader, the inefficiencies and waste in the parts and materials buying process results in technicians wasting at least a quarter of their time searching or shopping for parts.
Backed by sourcing and procurement expertise specific to facilities maintenance, repair and operations, FM supply chain technology enables technicians to better allocate their time and perform one-stop shopping for repair materials, eliminating the time-consuming exercise of going from supplier to supplier searching and ordering material required for repairs.
• Improved Wrench Time – Minimizes tech time spent searching for/shopping for/driving to parts suppliers
• First Call Completion – Inventory data and ordering of all parts & supplies through a single portal ensures technicians have accurate information on the parts needed and availability so, they complete work orders on the first visit, without having to come back to finish the job.
• Spend Leverage – Enables aggregation and leverage of spend and managed supplier performance (delivery, accuracy, price, etc.)
• Visibility & Control – Of all parts purchasing and supply chain
People, Process, and Technology to Support FM Objectives
To avoid technology becoming shelfware, it’s important to work with a solution provider that has the specialized people and proven process to ensure your FM supply chain technology works for your needs.
SDI has over 50 years of supply chain process excellence and deep category expertise to empower our customers to achieve their specific facilities management goals. The ZEUS digital supply chain platform creates critical transparency to anticipate demand, respond quickly to disruptions, and better identify savings opportunities. Our mobile application purpose-built for FM parts, IPM, enables multi-site FM’s to access to an extensive range of categories for maintenance/repair parts and store essential Goods Not for Resale (GNFR) that drives compliance to procurement protocols, yields enriched data for actionable insights, and provides full visibility across the enterprise for optimized labor and resource planning.
Read more about how SDI’s Integrated Parts Management solution can augment and enhance your FM strategy or contact us today.