Controlling supply chain costs is at the top of every manufacturing firm’s to-do list. While quick win strategies offer a few easy ways to capture value in the procurement process, only a comprehensive approach to MRO inventory can ensure processes are optimized and money is spent wisely. Often this means companies must overhaul their storeroom inventory management procedures and alter the way front-line employees, supervisors, and managers perform their jobs.
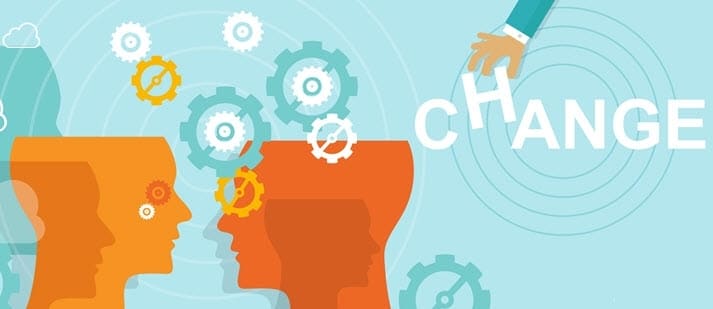
A detailed supply chain change management plan can help companies determine:
- what needs to be changed
- how to implement those improvements
- how to ensure employees adhere to the new directives
While we present these objectives separately, in practice, they are all interrelated, and their applications overlap throughout the MRO process.
Assessment of Current Storeroom Inventory Management
If your company is like so many others when it comes to storeroom management, you know your procurement practices are not as efficient as they should be, but you’re not quite sure why. This is not the time to reinvent your methods. Successful change management begins with an examination of how things are done now, how this formula developed, where it works and where it breaks down, where tasks take too much effort or time, and where waste occurs.
Next, evaluate your findings. Are the current methods outdated? If changes are made in one area, how will they affect operations up- and downstream? Change management in procurement requires consideration of other internal customers as well. You will need these people’s trust, confidence, support, and compliance throughout the changeover if your storeroom inventory management is to prove successful.
Gaining Buy-In from Your Team
Identifying problem areas and designing solutions are only the preliminary steps toward successful change management in the storeroom. The bigger challenge is winning the hearts and minds of:
- the executives who must approve the necessary investments
- the supervisors who will ensure new procedures are followed
- the storeroom employees who are ultimately responsible for process implementation
As with any significant change, initial resistance should be expected from every quarter. But you can motivate stakeholders to embrace change and welcome assimilate project goals as their own by employing these accepted change management practices:
Reassurance
When employees hear that changes are in the air, they naturally wonder what it means for them. They may need convincing that their jobs are not in jeopardy, but rather will be made more productive. Similarly, they may be suspicious that the coming changes are being undertaken on a mere whim and will be abandoned in a month. Successful change management must convince all stakeholders that the change is long-term, strategic, and well thought out. Do this by outlining the project’s scope and the objectives it will achieve.
Communication
With doubt and uncertainty come rumors. When workers do not know what changes are in store, they fill the void with worst-case scenarios. Fight disinformation with full disclosure. Provide regular updates to everyone in the organization, not just those who “need to know.” Present information often and in varied formats: Group discussions led by the supply chain management team (leave plenty of time for questions); newsletter articles documenting the project’s progress; regular emails from the CEO thanking workers for their patience during the transition. Be sure messaging reinforces the need for change, and why it is being made now. Be upfront if the change is transformative. Tell employees that the new system will entail some adjustments on their part; job descriptions may evolve, and new processes may need to be learned.
Inclusion
It is important to not only communicate goals and implementation strategies with all levels of the company, but also to include them in the decision making. This should be initiated even before the change is decided. Seek front-line employees’ input from the beginning. Encourage them to openly discuss – without fear of repercussions – where they feel improvements are needed and where, for convenience or work reduction, they break from established company procurement policies. Include representatives from all affected departments on the change management team. Pick forceful personalities. They will be outspoken about what is needed. More importantly, with a sense of ownership in the change, they will become outspoken proponents among their coworkers and peers.
Including these components in your storeroom inventory management changes will ensure greater acceptance among your workforce. Coupled with comprehensive training on the new procedures, this plan will give workers faith in the program and the confidence they need to use it as intended to bring about greater inventory accuracy, exception handling, fill rates and speed, and other hallmarks of an efficient storeroom. If you are still getting resistance from a certain department or person, read our blog post on how to overcome the naysayers.
Not sure if your company needs to improve your MRO storeroom processes or not? Learn more about the impact a clean and effective storeroom can have on your company.
Need help instituting a successful supply chain change management program in your MRO department? Contact SDI for a consultation.