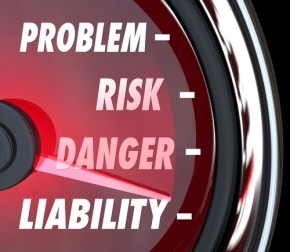
Maintenance, repair and operations (MRO) continues to be a tail-spend category for procurement teams, but a lack of focus on MRO could put your entire organization at risk. The benefits of MRO services extend beyond the acknowledged impacts on inventory control, spend under management, and efficiency. Embedding a strong MRO program also reduces risks related to production stalls, higher operations expenses, and potentially hazardous shop floor situations.
Therefore, MRO services from a qualified partner should become an integral part of procurement practices in order to reduce organizational risk.
Without properly managed MRO services, organizations encounter:
- Slower fill rates (due to stock-out of mission-critical parts)
- Increased returns (from poor inventory management and supplier communications)
- Reduced replacement efficiency (without the right part in the right location at the right time)
- Higher spend under management (because of weak supplier performance and maverick spending)
- Workplace hazards (from improper parts)
SDI has identified two primary risk areas that often occur due to poor MRO practices: compliance and top-line sustainability.
Compliance
With a decentralized supply structure where prices are negotiated at one level and transacted at another, site-level control can often enable rogue spending and put your organization’s compliance model at risk. At times, supplier contracts may be ignored in favor of relying on a local supplier.
Non-compliant parts can also put workers at risk. Although procurement may select parts that meet worker safety standards and conform to company policy, rogue orders can introduce lower quality parts. Without adequate MRO, procurement through non-designated supplier agreements can result in workplace safety violations and/or personal injury.
Top-line Sustainability
Production-line reliability is crucial to maintaining sales. Missing top-line expectations can consequently expose procurement issues. The procurement team can be on the hook when problems arise from stock-out or delayed third-party repairs following an unexpected stoppage. Production delays mean less time producing valuable products or can lead to hasty repair decisions that could end in further disruptions. All this can contribute to lower revenues and reduced output.
How Your MRO Service Provider Helps
In addition to addressing these issues, a well-managed MRO program, with the help of a MRO service provider, saves money. For example, your MRO partner can examine causes of common failure points to determine more sustainable operation. Instead of using new replacement parts each time a failure occurs, a part can be sent for repair, tracked, and returned like new for re-installation. By intelligently embedding an MRO-as-a-service provider into your procurement model, you can build an agile production organization that will operate in compliance, continue to produce uninterrupted, and save you money. SDI addresses your risks with well-managed, just-in-time MRO services.
To learn more about reducing compliance risk and sustaining top-line growth with better MRO solutions, contact SDI for a no-risk consultation.