In the early days of manufacturing, managers often relied on guesswork when adjusting their processes. Failures and missed opportunities were common, as tweaks to manufacturing and supply lines were frequently based on “gut feelings.” There were no reliable metrics for anticipating needs and predicting the outcomes of various adjustments.
Over time, the ability to collect and utilize actionable data has increased. Modern technology allows manufacturers to monitor every aspect of their processes in almost real-time. This data collection makes it possible to create empirical, quantifiable methods for removing defects from the production process chain.
The Six Sigma Methodology

Of all the methods for removing defects, Six Sigma is the most rigorous and widely recognized. Six Sigma is a set of techniques designed to identify and eliminate defects in a process, moving the overall process closer to perfection. Understanding that perfection is a goal, not a reality, Six Sigma aims for an overall defect rate of 3.4 per million opportunities.
Six Sigma uses quantifiable metrics and statistical modeling to break business processes down into small components. Data is then collected from each component, and scrutinized for defects. Once defects are identified, the metrics, statistical modeling, and data are then used to provide actionable methods for eliminating or minimizing those defects.
SDI has developed a Six Sigma Sourcing Methodology that uses the DMAIC model to improve results from a standard 7-step sourcing process. The added rigor and data driven philosophy of Six Sigma produces a repeatable and consistent outcome. The results from sourcing can often be debated as too biased by accepting a comfortable solution that may produce less than optimal results. Six Sigma forces decisions and improvements based on data-driven facts. Thus ensuring business stakeholders that the award recommendation made from a Six Sigma Sourcing project is the most optimal output considering all the variables.
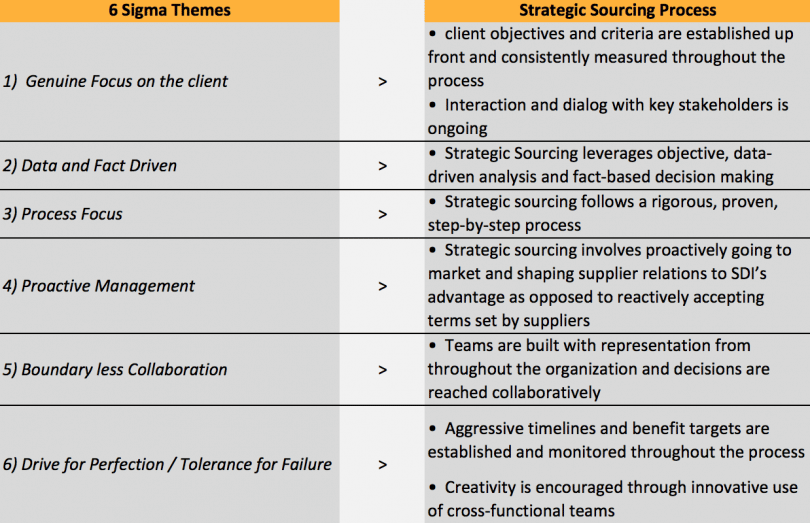
The Six Sigma Process
Supply chains are large, complex entities. Though this provides a lot of room for errors and defects to creep in; it also allows for a lot of opportunities for minimizing those errors and defects. To that end, SDI incorporates the Six Sigma DMAIC methodology into their sourcing process.
- Define: For any project to be successful, it must have clearly defined goals. This first step defines everything from sourcing groups and data needs, to the project team and timeline.
- Measure: Good data is crucial to Six Sigma methodology. At this step, data is carefully collected from the identified processes, according to the needs defined in the first step.
- Analyze: Meticulous examination of the collected data allows SDI to accurately assess bargaining position, establish strategies for improved sourcing, project potential savings, and more.
- Improve: Knowing where you need improvement doesn’t do any good unless you act on that information. At this step, SDI implements the necessary changes, including everything from planning negotiations to finalizing agreements with new suppliers.
- Control: Once defects are remedied, you want them to stay that way. The control step creates best practices for procurement, and establishes a system of continuous benchmarking to ensure that deviations are identified before defects occur.
Six Sigma Savings
Using the Six Sigma methodology, SDI is able to save clients money using a two-pronged approach. Identifying current defects allows SDI to offer solutions that reduce costs and improve supply chain reliability. By creating a repeatable, reliable system for supply chain improvement, SDI also helps clients avoid long-term costs associated with defects.
Connect with us today to learn about how SDI’s adherence to Six Sigma principles can improve your strategic sourcing process.