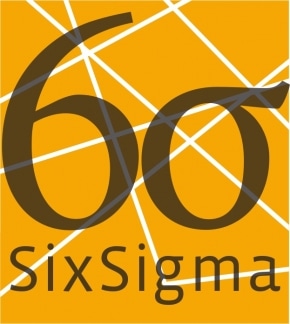
Six Sigma is a process improvement methodology that takes a scientific approach to resolving process problems, reducing errors and creating quality products, services, teams and organizations. It uses proven management tools that have been around longer than Six Sigma itself. Six Sigma brings those tools together in a systematic way to ensure that they work as intended. The ultimate goal of Six Sigma at SDI is to create a learning organization that can solve problems, innovate and provide value to its customers in the most efficient and effective way.
The Six Sigma method, abbreviated DMAIC, includes five phases;
D – define, M – measure, A – analyze, I – improve and C – control. Each phase has particular requirements that are met by deploying one or more of the appropriate management tools at the right time.
Today, I’m focusing on the Define phase and some of the tools that teams use during this phase.
D – Define: This initial phase is dedicated to planning and getting the clearest possible view of the problem, issue or process that needs to be addressed by the Six Sigma project. It is in this phase of the project that we seek the Voice of the Customer (VoC), figure out what is important to them, determine the potential costs and benefits of the project, establish the project charter, team, stakeholders, schedule etc. This phase is critical since the success of the project depends largely on the detailed planning that takes place in the beginning.
Some tools used in the Define phase are:
- VoC (voice of the customer – collected via surveys, interviews, complaint logs, etc.)
- Project Charter
- SIPOC (high level process map with information about customers, suppliers, inputs and outputs)
- SWOT (Strengths Weaknesses Opportunities Threats) analysis
- CTQ (Critical To Quality)
- FMEA (Failure Mode Effects Analysis)
- Process maps
- Value stream maps
- Business case
- Costs of Poor Quality analysis
Stayed tuned…Next time we’ll discuss the Measure phase!