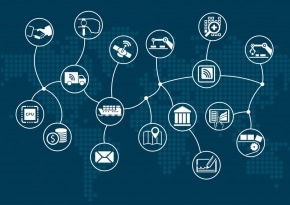
Manufacturers want to leverage evolving technology in the age of Industry 4.0. Companies that integrate their supply chain through digital technologies are agile and nimble. The digital supply chain allows them to improve service levels while cutting costs. Additionally, digital technologies provide enormous potential to develop new business models and adaptive strategies. But many companies are struggling to keep pace with the disruptive innovation that is changing the face of traditional supply chain management, while raising customer expectations to new heights.
Mid-market industrials are finding it harder to move beyond their older processes in MRO supply chain management to take advantage of advances in automation and the Industrial Internet of Things (IIoT). Manufacturers are limited in creating process improvements and delivering sustainable savings across the enterprise without supply chain integration, including:
- Connecting systems
- Improving data integrity
- Reducing the number of manual interventions in their processes
In order to take advantage of emerging technologies and stay competitive, manufacturers are looking at ways to improve standardization of data and systems which will enable the digitization of their MRO supply chain.
ISO 8000: For Data Integrity and Portability
Many manufacturers will go through a data capture and data cleanse process as part of their overall master data management. However, in order to utilize that data in their own systems, so they can buy the right materials every time and be able to leverage that spend, the information needs to be safely moved from one application to another. This is known as data portability. The ISO 8000 certification is the international standard for the exchange of quality data and information. It utilizes known Master Data Management concepts to standardize and structure data in a portable format. Quality, portable data will enable the digital supply chain. Standards like ISO 8000 are leading the industry to embrace data integrity and helping to usher mid-market industrials into Industry 4.0.
cGMP: To Ensure Quality
Current Good Manufacturing Practice or cGMP is the main regulatory standard for ensuring quality enforced by the Food & Drug Administration. Designed mainly for ensuring pharmaceutical quality, but also seen in the food and beverage manufacturing industry, cGMPs provide for systems that assure proper design, monitoring, and control of manufacturing processes and facilities. When a manufacturer adheres to cGMP regulations, they ensure the identity, strength, quality, and purity of their products by following a formal system of controls on the manufacturing operation. This ultimately prevents against contamination and errors, and ensures products meet quality standards. cGMP has very defined processes for certifying and validating that all software and systems associated with the manufacturing process are also in adherence to formal controls.
Because the technology and supply that SDI offers are involved in the manufacturing process, as a supply chain services provider, we require our systems go through a cGMP certification process to help our cGMP clients stay compliant. Before we connect to any pharmaceutical or cGMP food manufacturer’s system, we have to certify and validate the configuration of both the hardware and software associated with our platform connection, because it touches their system (ERP or CMMS) which is part of their cGMP processes. GMP regulators will audit the client to validate that all the documentation exists. SDI provides the documentation necessary to ensure our customer systems meet cGMP certification requirements and that the proper level of monitoring and follow up is in place to ensure the validity of our processes and systems.
SOC 1 Type 1 and Type 2: To Walk the Walk
SSAE 16, also known as the Service Organization Controls Report #1 (SOC 1) is an internationally recognized auditing standard developed by the American Institute of Certified Public Accountants (AICPA). The examination evaluates that controls are suitably designed to provide reasonable assurance that controls were designed to meet the established objectives. The controls addressed in SSAE No. 16 are those that SDI meets to prevent, or detect and correct, errors or omissions in the information it provides to clients or processes on their behalf. The type 1 examination verifies that the internal controls and processes are actually designed as the service organization intends, and that the controls are in place. Type 2 audits these processes to validate that the processes we said were in place, are in place. For example, data backed up on a predetermined basis. SDI is SOC 1 Type 1 and Type 2 compliant because not doing what we say, puts the client at risk. It’s important for us to commit to such a high level of standards for our clients, because as a cloud service provider, this helps ensure the client receives the desired outcomes.
It’s important for any cloud-based provider to demonstrate its commitment to providing customers with the highest standards in processes, controls, and procedures, enabled by quality data. The digitization of the MRO supply chain depends on it. By having these certifications, it allows mid-market industrials and manufacturers to quickly adopt cloud-based services and embrace the digital supply chain without having to invest the resources to build it internally, and without the fear of risk by assuring that the proper controls are in place to support their business. Allowing for supply chain integration in a way that is agile, nimble, with speed to execution, and providing any organization the ability to shift on a dime. Most importantly, it allows customers to adopt new strategies safely without the fear of the unknown becoming an impediment to change and progress.